Coating removal to enable riser upgrades
Overview
With a platform in the Caspian Sea soon to be upgraded with three new risers, McDermott contracted Ashtead Technology to efficiently remove the coating from the horizontal and vertical jacket members so that an SA2.5-quality surface finish could be achieved.
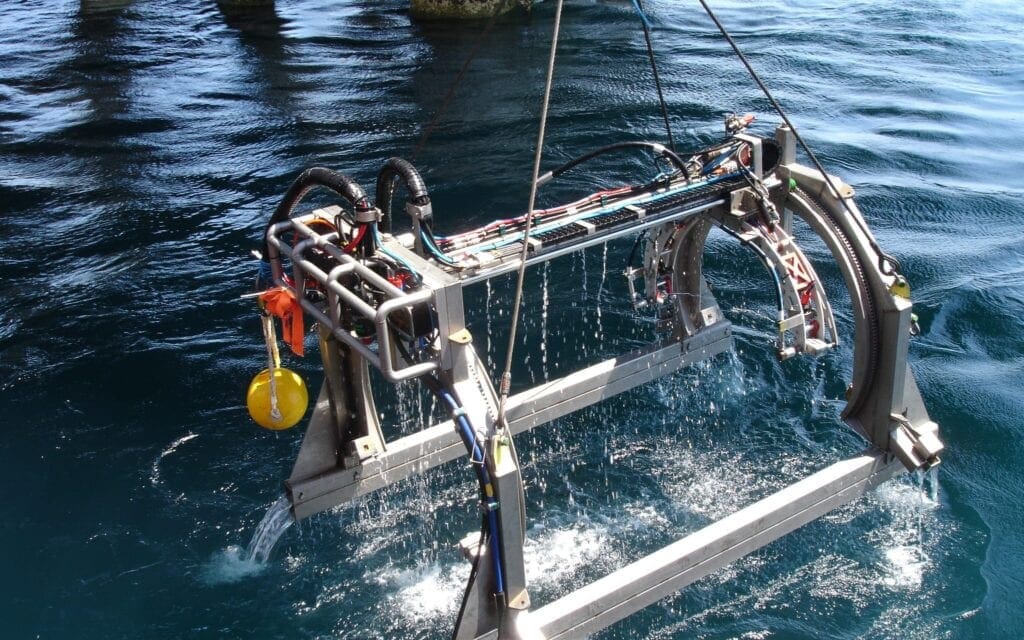
Solution
Ashtead Technology’s Mechanical Solutions teams are highly experienced in ensuring customers achieve maximum productivity from their subsea assets and have a long-established track record in the design and development of coating removal solutions.
Due to variances in the size of subsea members to be cleaned, ranging from 700 – 1500mm in diameter and 1200 – 9000mm in length, the operating system had to be versatile enough to be rapidly reconfigured as required.
Ashtead Technology designed and engineered three bespoke Coating Removal Tools (CRT), as well as the necessary Control Cabin and Supervisory Control and Data Acquisition (SCADA) Control Operating System required to utilise the equipment, in only 10 weeks.
With an innovative dual-nozzle design halving the debris removal time, the CRT is controlled by technicians topside using a bespoke SCADA control system. This enables the operators to see a graphical representation of the location on the pipe; an essential performance enhancement in poor underwater visibility situations.
The CRT removes all types of protective coatings including concrete weight coat, epoxy, bitumen and FBE on subsea pipelines and platform jacket members. The system utilises high-pressure water, with the capacity to clean structures with diameters of 152mm to 1500mm.
Benefits and value
Prioritising ease of use, Ashtead Technology developed an operating system which could be partially or fully-automated depending on the customer’s immediate requirements.
Following a comprehensive series of yard-based trials, operations in the Caspian Sea were successfully completed, further underlining the value of the CRT concept in harsh marine environments.
With underwater cameras and related technologies giving real-time positioning information in graphical format, the CRT’s two opposing high-pressure water jets sweep and clean the product. Linear, rotational, nozzle standoff and sweep speeds are controlled topside by specialist Ashtead Technology technicians.
The CRT is also able to clean a workspace of 1.5 metres in a linear pass before needing to be repositioned, outperforming comparable technologies. Any size or shape of area within this 1.5 metre area, including the full 360-degree circumference of a tubular, can be cleaned.

Testimonial
“Our team has supported decommissioning, inspection, repair and maintenance projects offshore for nearly two decades. Using our in-house engineering capability, our client benefited from a custom-built solution which in turn become something we could offer more widely to the market.”
Richard Lind
General Manager, Mechanical Solutions